Mincon MQ68 Hammer
The Mincon MQ68 hammer is designed around proven technology to perform at the top end of the performance scale compared to other tools on the market. These tools are excellent for all types of drilling applications including residential geothermal, production quarry drilling, seismic drilling and small construction drilling.
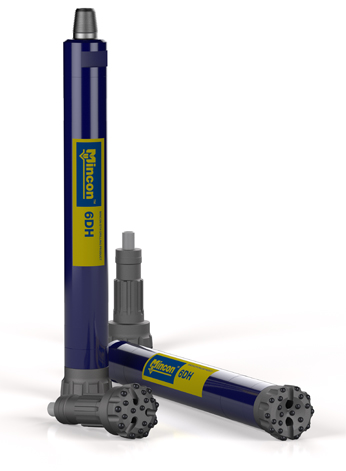
Key Features and Benefits
- Patented features maximize energy output and reduce service requirements.
- Fewer internal components minimize service requirements.
- Valveless, high frequency design ensures smooth operation.
- Hardened wear sleeve for optimum wear resistance even in the most abrasive conditions.
- Multi-start threads on backhead and chuck ensure easy coupling/uncoupling of hammer.
- Unique internal mount system eliminates the need for wear shims and special assembly tools.
- All critical internal components are heat treated under strict control to maximize tool longevity.
For more information:
+40 314 253 800
info@romned.ro
Ron van Dam
CEO
Specifications | Metric | Imperial |
Hammer Outside Diameter | 146mm | 5.75″ |
Hammer Length (Less Bit, Backhead Shoulder to Chuck) | 1002mm | 39.4″ |
Backhead Spanner Flat Size | 100mm | 4″ |
Drill Bit Shank Type | QL60 | |
Minimum Bit Size | 152mm | 6.0″ |
Hammer Weight (Less Bit) | 87.9Kgs | 194Lbs |
Drill Bit Weight (165mm/6 1/2″) | 24.5Kgs | 54Lbs |
Piston Weight | 19.3Kgs | 42.5Lbs |
Backhead Stand Off | 0.75mm | 0.030″ |
Make up Torque | 6100-8135 NM | 4500-6000 FT Lbs |
Wear Sleeve Reverse Limit | Non Reversible | |
Wear Sleeve Discard Limit | 128.5mm | 5.060″ |
Recommended Minimum Air Package | 283 l/s @ 20.7 Bar | 600 cfm @ 300 psi |
Item # | Part Number | Description |
MC601AS01 | Mincon MQ68 (3 1/2″ A.P.I. Reg. Pin) | |
1 | MC601BH01 | Backhead (3 1/2″ A.P.I. Reg. Pin) |
2 | MD622OR01 | O Ring |
3 | MB506CH01 | Choke Blank |
4 | MB502CV01 | Check Valve |
5 | MB503SP01 | Spring |
6 | MB504SM01 | Steel Make-Up Ring |
7 | MB505LR01 | Lock Ring |
8 | MC603LM01 | Lock Ring Mount |
9 | MD607DR01 | Air Distributor |
10 | MD621OR01 | O Ring |
11 | MD620OR01 | O Ring |
12 | MC609SR01 | Seating Ring |
13 | MC608IC01 | Inner Cylinder |
14 | MC610PN01 | Piston |
15 | MC611WS01 | Wear Sleeve |
16 | MC612PR01 | Piston Retaining Ring |
17 | MD622OR01 | O Ring |
18 | MD622OR01 | O Ring |
19 | MC613BB01 | Aligner |
20 | MC614BR01 | Bit Retaining Ring |
21 | MD621OR01 | O Ring |
22 | MC615CK01 | Chuck (QL60) |
23 | MD626SK04 | Service Kit |
MD626SK04 | Service Kit | |
3 | MB506CH01 | Choke Blank |
MB506CH02 | Choke 1/8″ (3.2mm) | |
MB506CH03 | Choke 3/16″ (4.8mm) | |
5 | MB503SP01 | Spring |
MD625OK04 | O Ring Kit | |
MD625OK04 | O Ring Kit | |
2 | MD622OR01 | O Ring |
10 | MD621OR01 | O Ring |
11 | MD620OR01 | O Ring |
17 | MD622OR01 | O Ring |
18 | MD622OR01 | O Ring |
21 | MD621OR01 | O Ring |
Air Pressures are given for compressors operating at seal level at 20° C (68º F). Corrections to actual compressor volume should be made to account for temperature, altitude and relative humidity.
DTH hammers must receive a constant supply of proper rock drill oil to protect the internal components and to provide a good air seal between the hammer’s running surfaces for efficient drilling. Mincon recommends the use of Mincon Envirosafe® Rock Drill Oil (RDO) to maintain optimal performance and extend the life of the internal components. The correct consumption of oil is dependent upon the air volume and conditions. Please refer to the lubrication graph below for recommendations. When drilling in wet conditions the normal amount should be doubled. There should be visual evidence of oil around the drill bit shank and within the tube joints when changing tubes.
If using petroleum based rock drill oils, the recommended grade of oil is dependent on the ambient temperature and the operating pressure. As a rule of thumb, ISO320 grade rock drill oil should be used whenever possible as the hammer is a high frequency tool, however, where the pump cannot pump the oil in colder conditions, a lower grade of oil can be used as per the graph below.
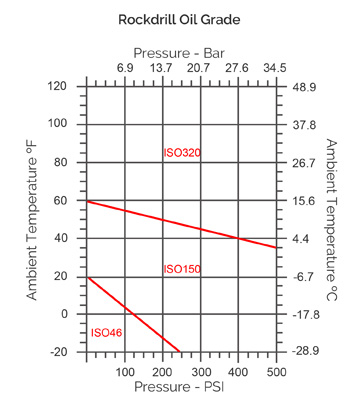
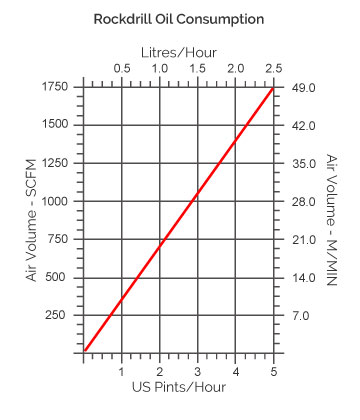
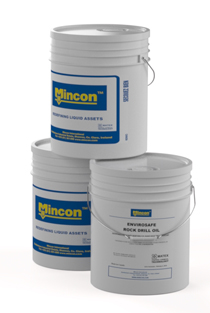
Note: The Part Numbers below require the Carbide Insert type code to be added on the end to complete them. For a combination of carbide inserts use the gauge row code first and then the face code.
Diameter | Face Type | Part Number | No. x Button Dia (inch) | Flushing holes | Weight Approx. | ||||
mm | inch | Outer | Inner | Front | Kgs. | Lbs. | |||
159 | 6 1/4 | Concave | 62QL60C58 | 8 – 5/8 | 4 – 5/8 | 4 – 5/8 | 2 | 23.6 | 52 |
159 | 6 1/4 | Concave | 62QL60C38 | 8 – 3/4 | 4 – 5/8 | 4 – 5/8 | 2 | 24.1 | 53 |
165 | 6 1/2 | Concave | 64QL60C58 | 8 – 5/8 | 4 – 5/8 | 4 – 5/8 | 2 | 24.5 | 54 |
165 | 6 1/2 | Concave | 64QL60C335 | 8 – 3/4 | 4 – 3/4 | 4 – 5/8 | 2 | 25 | 55 |
165 | 6 1/2 | Flat Face | 64QL60F38 | 8 – 3/4 | 8 – 5/8 | 2 | 25 | 55 | |
165 | 6 1/2 | Convex | 64QL60V359 | 9 – 3/4 | 4 – 5/8 | 4 – 5/8 | 3 | 25 | 55 |
171 | 6 3/4 | Concave | 66QL60C58 | 8 – 5/8 | 4 – 5/8 | 4 – 5/8 | 2 | 25.4 | 56 |
171 | 6 3/4 | Concave | 66QL60C335 | 8 – 3/4 | 4 – 3/4 | 4 – 5/8 | 2 | 25.4 | 56 |
171 | 6 3/4 | Concave | 66QL60C39 | 9 – 3/4 | 6 – 5/8 | 5 – 5/8 | 3 | 25.4 | 56 |
171 | 6 3/4 | Convex | 66QL60V359 | 9 – 3/4 | 4 – 5/8 | 4- 5/8 | 3 | 25.4 | 56 |
171 | 6 3/4 | Flat Face | 66QL60F30 | 10 – 3/4 | 12 – 5/8 | 2 | 25.4 | 56 | |
178 | 7 | Concave | 70QL60C39 | 9 – 3/4 | 6 – 5/8 | 5 – 5/8 | 3 | 26.3 | 58 |
178 | 7 | Flat Face | 70QL60F39 | 9 – 3/4 | 11 – 5/8 | 3 | 26.3 | 58 | |
190 | 7 1/2 | Concave | 74QL60C39 | 9 – 3/4 | 6 – 3/4 | 5 – 3/4 | 3 | 30.4 | 67 |
190 | 7 1/2 | Flat Face | 74QL60F39 | 9 – 3/4 | 11 – 3/4 | 3 | 30.4 | 67 | |
197 | 73/4 | Concave | 76QL60C50 | 10 – 5/8 | 4 – 5/8 | 8 – 5/8 | 2 | 32.7 | 72 |
200 | 7 7/8 | Concave | 77QL60C39 | 9 – 3/4 | 6 – 3/4 | 5 – 3/4 | 3 | 33.6 | 74 |
200 | 7 7/8 | Convex | 77QL60V39 | 9 – 3/4 | 6 – 3/4 | 5 – 3/4 | 3 | 33.6 | 74 |
203 | 8 | Concave | 80QL60C30 | 10 – 3/4 | 6 – 3/4 | 7 – 3/4 | 2 | 34.1 | 75 |
203 | 8 | Convex | 80QL60V39 | 9 – 3/4 | 6 – 3/4 | 6 – 3/4 | 3 | 34.1 | 75 |
216 | 81/2 | Concave | 84QL60C30 | 10 – 3/4 | 7 – 5/8 | 12 – 5/8 | 2 | 35.9 | 79 |
219 | 8 5/8 | Concave | 85QL60C30 | 10 – 3/4 | 6 – 5/8 | 12 – 5/8 | 2 | 36.8 | 81 |
222 | 8 3/4 | Concave | 86QL60C30 | 10 – 3/4 | 6 – 5/8 | 12 – 5/8 | 2 | 36.8 | 81 |
- Mincon 6″ Range Brochure
- Mincon MQ68 Operation and Service Manual
- Mincon DTH Tools Product Catalogue